CoolantLoop Recycling System
Part #: TBD
Get Started
Request A QuoteStill Have Questions?
Contact Us- The CoolantLoop can be used with virtually any coolant.
- Our continuous recirculation of the system which eliminates stagnation, provides aeration, and gives multi-pass filtration.
- Because of our open-channel coalescing technology, our system will not split weak emulsions or remove additive packages like other technologies.
Instrument Air | Input Power | Process Pressure |
---|---|---|
30 PSI (2.07 bar) |
120 V (240V Avaiable on Request)
|
40 PSI (3 bar) |
FAQ Coolant Recycling Questions
Explore SmartSkim ProductsSome of the older technology that emulsifies the tramp oils may not be a good candidate, but almost all synthetic, semi-synthetic, and soluble oil coolants have seen great success.
- Shops that have multiple metal working machines with stand alone coolant sumps
- Small shops with as few as 5 -10 machines
- Large shops with hundreds of machines
New coolant concentrate savings are generally 30% - 65% of previously purchased coolant. Factors that affect the final number include whether the customer is draining chips, concentration control, and dump schedule.
If you don’t haul away the current volume of coolant and instead recycle it you will in effect not have to replace that coolant with new coolant.
Typical customer savings range from 50% - 90%.
If treating in house, there are labor costs associated. If hauling, you will need to include any and all truck charges, fuel surcharge, other fees to determine savings.
Related Resources
Learn more about how the CoolantLoop Recycling System can benefit your application with the following resources.
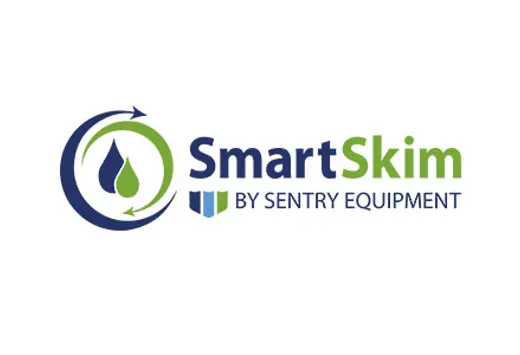
Calculate Your Savings
Estimate your Coolant Recycling Savings by adopting a CoolantLoop system with our ROI Calculator.
Browse All Resources
Explore more information on SmartSkim products and services in our Resource Library.